If you’ve ever wondered how scales accurately measure weight, load cells are the unsung heroes behind the scenes. But what are load cells, and how do they work? Read on to learn about the pivotal role load cells play in weighing instruments.
What Is a Load Cell
Load cells are small devices used in scales to convert force or weight into an electrical output. There are different types of load cells, each with its own unique specifications and applications. Strain gauge load cells are the type most commonly found in industrial scales.
How Do Load Cells Work?
Load cells use material like wire or foil that changes shape when force (the weight of an object) is applied to it. The change in shape, or deformation, creates an electrical signal that can be measured and converted to weighing data. Unless overloaded, the load cell will return to its original shape once the object is removed from the scale.
In more detail, here’s a simple rundown on how strain gauge load cells work:
- Deformation: You place an object on the scale, and the force of the object’s weight is applied to the load cell(s). This force slightly deforms the load cell’s material.
- Strain Gauge:Â Attached to the deforming material are tiny electrical resistors called strain gauges. These resistors change their resistance when they stretch or compress.
- Change in Resistance:Â As the load cell material deforms, it causes the strain gauges to stretch or compress, changing their resistance. This resistance change corresponds to the weight applied to the scale.
- Electrical Signal: The load cell connects to an electrical circuit that monitors the strain gauges’ change in resistance. The change is converted into a voltage or current.
- Weight Calculation: The voltage or current is used to calculate the object’s weight based on the known relationship between the force applied to the load cell and the change in the strain gauges’ resistance.
- Display: The calculated weight is displayed on the scale’s screen in a common unit of measure like pounds or grams.
Load Cell Accuracy
When installed and calibrated correctly, load cells are extremely accurate. There’s a reason why almost all electronic scales today — from basic kitchen scales to heavy-duty industrial scales — use some type of load cell. If they weren’t accurate, we would use a different, more reliable technology for weighing.
Signs a Load Cell Needs to Be Replaced
Load cells are crucial components in scales, but they can wear out or lose their accuracy over time. Signs there may be something wrong with your load cells include:
- The scale won’t return to zero. If you overloaded your load cell, it may be misshapen, which will prevent the scale from returning to zero after you remove the object. Overload damage is often permanent, and you will likely need to replace your load cell.
- You receive inconsistent readings. If your scale is consistently giving you different readings for the same item, there may be an issue with the load cells. Depending on the problem, you may be able to calibrate the load cell or you may need to replace parts.
- The load cell is physically damaged. If the load cell is cracked, dented, bent, or otherwise damaged, its performance might be impaired.
- You frequently have to recalibrate your scale. Scales need routine calibration services to ensure accurate weighing data. However, if your scale constantly needs to be calibrated or fails to calibrate correctly, there could be a load cell issue.
- Your scale has zero drift. Zero drift is a gradual change in the zero reading over time, even without weight on the scale. The load cell may no longer be stable and need replacement.
If you notice any of the above issues, you should contact your local industry expert for assistance. They should be able to help you determine if the load cell needs to be replaced or if you can get away with repair or calibration services.
Quality Scales with Quality Load Cells
The load cell might be the most important part of a scale, so you want to ensure you have scales that start with a foundation of quality, reliable load cells. At UniFide CST, you can find high-quality industrial scales from brands you can trust, like Mettler Toledo and Rice Lake. Whether you need a floor scale, counting scale, truck scale, or something else, we have the right solution for you. Get a quote today.
More Blog Posts
Why Do Trucks Get Weighed?
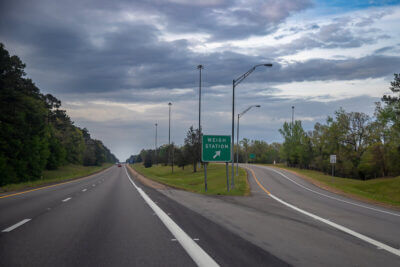